Predictive Maintenance
Maschinen und Anlagen vorausschauend warten, Ausfallzeiten minimieren und Laufzeiten maximieren
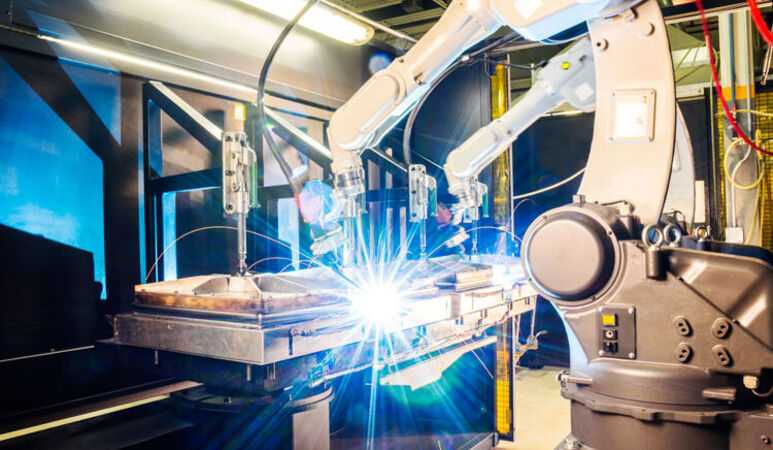
Predictive Maintenance nutzt digitale Möglichkeiten, um die Laufzeiten von Maschinen und Anlagen in der Produktion zu optimieren. Das Verfahren fußt im Wesentlichen auf zwei Teilbereichen der Künstlichen Intelligenz (KI):
- Data Mining: Bei Predictive Maintenance wird dafür mithilfe von Sensoren der Zustand einer Anlage oder Maschine fortlaufend in Form digitaler Daten erfasst und damit kontinuierlich überwacht (engl. „condition monitoring“).
- Predictive Analysis: Die erfassten Daten werden durch (lernende) Algorithmen automatisch analysiert. Die Algorithmen suchen dabei vor allem nach Mustern, die auf Unregelmäßigkeiten, Verschleiß oder Qualitätsverluste hinweisen, sodass die Eintrittswahrscheinlichkeit von Ereignissen wie etwa der drohende Ausfall der Maschine berechnet und vorhergesagt werden kann.
Durch die Verbindung dieser beiden Teilbereiche der KI wird eine „vorausschauende Wartung“ (engl. „predictive maintenance“) möglich. Der größte Vorteil von Predictive Maintenance ist, dass eine Wartung nur noch dann vorgenommen wird, wenn die Reparatur zwingend notwendig ist. Auf feste Wartungsintervalle, die im schlimmsten Fall mögliche Schäden nicht rechtzeitig erkennen, kann auf diese Weise verzichtet werden. Im Ergebnis werden so die Ausfallzeiten von Maschinen und Anlagen minimiert sowie deren Laufzeiten maximiert. Predictive Maintenance dient daher vor allem dazu, die Produktivität und damit auch die Wettbewerbsfähigkeit von Unternehmen zu optimieren.
Predictive Maintenance wird sich in der Produktion durchsetzen
Während im Handel, in der Werbung, in sozialen Medien und auf Streaming-Plattformen bereits maschinelle Lernverfahren zur vorausschauenden Analyse des Kundenverhaltens und in der Folge für bessere Angebote genutzt werden, sind Data Mining und Predictive Analysis in der industriellen Produktion noch nicht so weit verbreitet. Zwar wünschen sich die meisten Unternehmen (93 Prozent) aus dem Maschinen- und Anlagenbau sowie der Elektro- und Automobilindustrie den Verschleiß von Anlagen automatisch und rechtzeitig zu erkennen, jedoch gaben in der gleichen Umfrage lediglich 37 Prozent der befragten Unternehmen an, die Methode der vorausschauenden Instandhaltung bereits zu nutzen.
Die Umfrage ergab zugleich, dass mehr als acht von zehn Unternehmen, die bereits Predictive Maintenance einsetzen, damit gute bis sehr gute Erfahrungen gemacht haben. Das Verfahren dürfte sich daher in den kommenden Jahren weiter durchsetzen und hat gerade im Kontext der Vision von Industrie 4.0 das Potenzial, zu einem industriellen Standard heranzureifen. Wer sich frühzeitig mit dem Thema beschäftigt, sichert sich dadurch Wettbewerbsvorteile. Das gilt vor allem hinsichtlich des Aspekts, dass die eingesetzten Techniken auch auf Erfahrungswerten beruhen.
Wie eingangs erwähnt, kann der Zustand von Anlagen und Maschinen nur durch eine kontinuierliche Erhebung der Betriebsdaten überwacht werden. Bei der Analyse dieser Daten geht es anschließend darum, zu identifizieren, was „normales“ Maschinenverhalten ist. Die Klassifikation, welches Maschinenverhalten unauffällig ist oder aber kurz-bis mittelfristig zu einem Ausfall führen kann, wird also allein anhand der Betriebsdaten der Maschinen oder Anlagen durchgeführt.
Um das zu gewährleisten, muss zunächst eindeutig festgelegt werden, welche Maschinenzustände als Ausfälle zu werten sind. Im nächsten Schritt gilt es, Variablen beziehungsweise Attribute zu bestimmen, anhand derer beobachtet werden kann, wie sich das System verhält. Im Machine Learning werden diese Variablen als „Feature“ bezeichnet. Um Feature-Daten zu erhalten, werden bei Maschinen und Anlagen Sensoren eingesetzt, die diese Variablen beziehungsweise Attribute messen und festhalten. Welche Typen von Sensoren dabei verwendet werden, wo sie auf der Anlage positioniert sind und in welchen zeitlichen Abständen sie Daten erheben, beeinflusst nicht nur die Qualität der Daten, sondern ist auch entscheidend für die Vorhersagequalität der Algorithmen. Dieser Prozess wird Feature Engineering genannt. Da es stets um den Einfluss unterschiedlicher Variablen auf eine konkrete Anlage oder Maschine geht, muss das Feature Engineering zwingend anwendungsspezifisch erfolgen. Mithilfe der Features können die Algorithmen also letztlich auf ihre spezifische Aufgabe im individuellen Anwendungsfall trainiert werden.
Aufbau eines Datenpools
Berücksichtigt man, dass die Zustandsüberwachung allein auf der Analyse von Zeitreihen der Betriebsdaten beruht, leuchtet sofort ein, dass für eine entsprechende Güte der Überwachung auch quantitativ genügend Betriebsdaten verfügbar sein müssen. Dabei steigt der Datenbedarf mit der Komplexität des beobachteten Systems. Konkret heißt das beispielsweise, je mehr variable Eingangsgrößen oder Konfigurationen für ein System existieren, desto mehr Betriebsdaten der Maschine oder Maschinen gleicher oder zumindest ähnlicher Bauart müssen bereitgestellt werden, um eine verlässliche Überwachung zu gewährleisten.
Dabei ist nicht nur die reine Datenmenge wichtig, sondern auch, dass hinreichend viele Maschinenausfälle im Datenpool enthalten sind. Häufig sind jedoch gerade solche Daten nur eingeschränkt vorhanden, insbesondere, wenn teure Maschinen oder Anlagen zuvor zu festgelegten Zyklen und vergleichsweise konservativ gewartet wurden. In solchen Fällen können zum Beispiel mechanistische Modelle herangezogen werden, um Maschinenausfälle zu simulieren und entsprechende Pseudo-Betriebsdaten zur Verfügung zu stellen.
Die Entscheidung zur Instandhaltungsmaßnahme trifft am Ende immer noch ein Mensch
Im Falle eines auffälligen Maschinenverhaltens muss im Rahmen der vorausschauenden Instandhaltung der richtige Zeitpunkt für eine möglichst kosteneffiziente Wartung geplant werden. Dafür muss vor allem verlässlich geschätzt werden, wie lang der Fortbetrieb einer Maschine oder Anlage noch möglich ist, ohne dass dies negative Folgen für den Maschinenzustand oder angeschlossene Prozesse hat. Hier sind je nach Datenlage technisch geringfügig unterschiedliche Ansätze der Mustererkennung aussichtsreich. In jedem Fall wird dabei aber algorithmisch das gemessene Maschinenverhalten verglichen mit dem Verhalten, das im Vorfeld bei dieser oder vergleichbaren Maschinen beobachtet wurde.
Auf Basis der geschätzten „Restlaufzeit“ der Anlage wird jedoch die verantwortliche Person in die Lage versetzt, eine faktenbasierte Entscheidung treffen zu können, wann Instandhaltungsmaßnahmen sinnvollerweise vorzunehmen sind. Für die Planung der Wartung ist zu beachten, dass der Wartungsprozess selbst ebenfalls Kosten verursacht, zumal hierfür in der Regel der Maschinen- oder Anlagenbetrieb vollständig eingestellt werden muss. Letztlich bleibt es dem Betreiber überlassen, ob er eine mehr oder weniger konservative Strategie verfolgen möchte.
Predictive Maintenance für ältere Maschine – „Retro-Fit-Lösungen“
Aus wirtschaftlichen Gründen müssen Maschinen in der Produktion möglichst über viele Jahre laufen. In den Unternehmen finden sich daher zahlreiche Maschinen, die nicht mit Sensoren ausgestattet sind und auch keine Schnittstellen zu digitalen Systemen besitzen. Für diese älteren Maschinen und Anlagen gibt es jedoch mittlerweile sogenannte „Retro-Fit-Lösungen“. Die Maschinen und Anlagen werden dabei mit entsprechender Technik nachgerüstet. Das lohnt sich in der Regel nicht nur mit Blick auf die Einführung von Predictive Maintenance. Die Vereinheitlichung von Standards und aufeinander abgestimmte Softwarelösungen trägt auch dazu bei, die Bedienung der Maschinen zu erleichtern. Nähere Informationen dazu bietet beispielsweise das Mittelstand 4.0 Kompetenzzentrum eStandards.